衬套(见图1)是分配机构中的关键部件,其加工的精度直接影响液压机构的运行状况,从而影响操纵的稳定性。
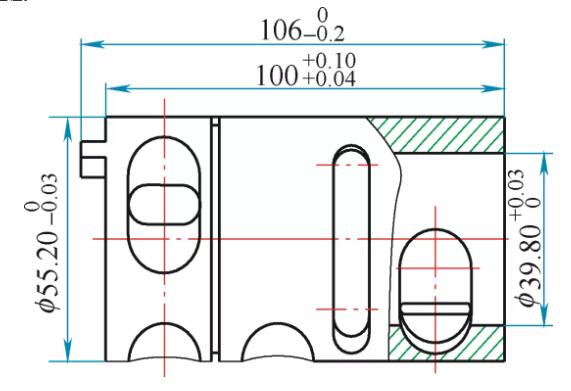
图1 衬套结构
1.问题的提出
衬套的热处理要求:进行氮化处理,氮化层0.3~0.6mm,硬度≥600HV。衬套经氮化处理后,在部件的装配过程中,发现个别零件出现了掉块现象。经过检查,掉块均在尖角和边角处出现。为了探究掉块的原因,随机在零件的掉角处进行了线切割加工,取样进行金相组织检验。零件试样在进行金相检验时,发现氮化组织中出现了网状氮化物(见图2)。按照GB/T11354——2005《钢铁零件渗氮层深度测定和金相组织检验》中的规定,评定氮化物网状组织达到了5级,属于严重不合格组织。
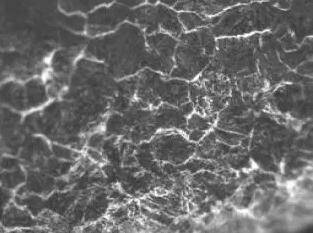
图 2
2.原因分析由于氮化生产我们是首次进行,这方面的经验不是很多,通过咨询和查阅资料,分析产生此种异常组织的原因主要是:在渗氮生产过程中,炉内的氮势过高,造成零件的表面氮原子聚集,先渗入的氮原子没能及时向零件内部扩散,随着零件表面渗入的氮原子不断增加,在零件的表面聚集越来越多,最终逐渐形成了网状组织。这种情况往往会出现在零件的尖角和锐边,零件的实际情况也是如此。推断氮化过程中出现氮浓度过高的原因大致有以下几种原因:
(1)渗氮过程中,炉内的氨分解率出现了波动,没能及时调整,或设备状况出现异常,都有可能影响炉内的渗氮气氛,从而导致零件表面出现非正常的组织。
(2)渗氮开始时,炉内在建立起必要的浓度梯度后,氮原子通过表层向内部进行扩散。而当炉内的氨分解率出现波动时,在随后的扩散过程没能及时进行调整,炉内的氮势高,势必造成了在零件表面聚集大量的氮原子,并逐渐形成了网状组织。
(3)由于零件表面的氮势过高,在冷却过程中也易出现脆性相,使渗层脆性增加。
(4)零件边角若毛刺、锐边过大,氮化过程中也会增加了氮原子聚集的倾向,从而出现网状组织。
(5)液氨的含水量过高,影响氮化过程中炉内的氮化气氛,即炉内的杂质多,也会影响氮化的质量。
3.氮化工艺的改进及效果
根据以上的原因分析,在随后的氮化工艺运行中,将工艺进行了适当变动,主要有以下几点:
(1)氨分解率是渗氮工艺过程中一个重要参数,它的高低直接影响工件表面的吸氮速度。氨分解率对渗层硬度及层深的影响,主要表现在渗氮开始的几小时或十几小时内。因此,渗氮初期选用较低的氨分解率(即足够高的炉气氮势),将强渗阶段的氨分解率调整为33%,以便在较短时间内建立起必要的浓度梯度;扩散阶段的氨分解率调整为55%,这样做的目的就是降低氮化炉内的氮势,减少零件的氮化组织出现氮化物级别增高的可能性,并适当地降低零件的氮化硬度。
(2)为了预防ε相脆性过大而不合格,将氨分解率调整为80%以上,进行退氮处理和扩散处理,目的是降低氮化炉内的氮势,控制零件表面的氮浓度,从而保证零件的氮化组织不出现严重的网状组织。
(3)为了避免零件在氮化过程中边角处出现氮化物聚集的现象,将零件进行镀锡处理,并严格控制零件的镀锡层厚度,保证镀锡层的厚度在0.004~0.008mm。若镀锡层镀薄,则不会起到防渗作用;镀层过厚,在氮化时,镀锡层就会出现流淌现象,影响氮化面的氮化质量。经过试验,镀锡层的厚度控制在0.004~0.008mm,防渗效果是最好的。
(4)选用GB536—1988《液体无水氨》中规定的浓度为99.9%的液氨,避免氨气在进入炉内产生水汽,从而影响炉内的氮化效果。
(5)将输气方式由原来的单瓶连接变为汇流排连接,这样就能有效地避免换液氨瓶时出现杂气浑入炉内的现象,从而保证了氨气供应的连续性。
(6)根据氮化过程的各阶段的实际情况,适时地调整设备的排气开关,控制氨气的流量,调节炉气压力,以保证炉内的氮势控制在合理的范围内。
(7)根据零件的装炉数量,适时延长氮化的保温时间,从而更好地保证氮化层深度。
通过采取以上几种有效的技术措施,并在实际生产中,控制氨分解率的大小,逐渐摸索出了解决氮化问题的办法,零件的氮化效果得到了很大的提高。经过金相检验,氮化组织中没有发现网状氮化物,完全符合GB/T11354—2005《钢铁零件渗氮层深度测定和金相组织检验》中规定的要求,能够达到二级,脆性检查1级,零件的氮化硬度控制在780~840HV,完全符合图样中的技术要求(见图3)。
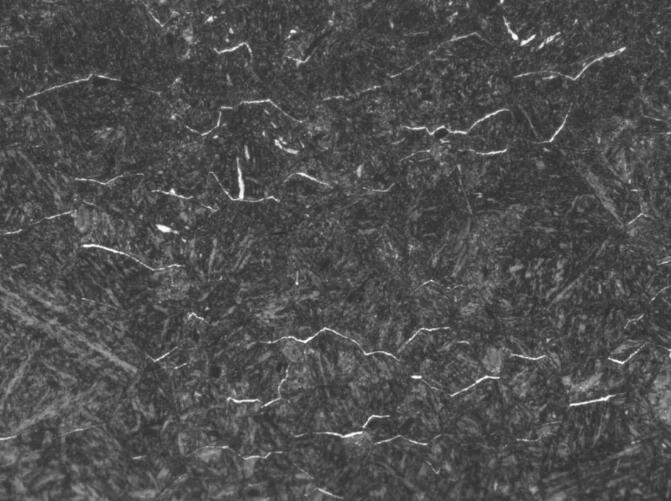
图 3
氮化后的零件在随后的磨削工序和装配过程中,均没有发现掉块、裂纹等缺陷。经过试生产解决了氮化过程中出现的氮化组织不合格、防氮化物聚集的镀锡层流淌等问题,从而保证了生产的正常进行。4.结语
零件在进行氮化处理时,由于氮化介质氨气质量不稳定,氮化炉内的氨分解率的不稳定,直接影响氮势的稳定性。如果不及时调整氨气的流量,氨分解率不能及时得到控制,零件的氮化组织就会出现不合格现象,导致零件出现废品。因此在氮化过程中,要实时监控,严格控制温度、氨分解率等工艺参数,保证氮化工艺的正常运行。
- 上一篇:模具气体氮化硬度低的原因及应对方法
- 下一篇:QPQ处理对40Cr钢渗层组织的影响