离子渗氮工艺对设备是有基本要求的,主要包括:
(1) 真空度:设备的真空炉体必须具有良好的密封性能,由真空获得系统来保证。真空获得系统由两台旋片式机械真空泵、真空电磁阀、电动真空蝶阀、真空检测装置等组成,通过真空管道与真空炉体连接。炉体的真空度用压升来衡量,压升的标准为≤0.13 MPa /min。
(2) 绝缘性:阴、阳极之间必须要有良好的电绝缘性能,才能保证工艺正常进行和设备安全。阴极输电装置由阴极杆、密封件、绝缘垫、承重柱和气隙套组成,阴极引线通过阴极输电装置与阴极盘相联。
(3) 良好的灭弧性能:在工艺过程的不同阶段,零件表面会不同程度地产生弧光放电(俗称“打弧”) ,零件表面清洁阶段和升温阶段表现最为明显,到了保温也就是辉光稳定后,偶尔也有辉光向弧光转变的情况。打弧的主要特点是低电压、大电流放电,对于电源来说类似于短路,所以要求设备具有良好的灭弧性能,保护零件和设备不被损坏。
(4) 水冷却:真空炉体设计循环水冷却,是为了延长橡胶密封件等的使用寿命,避免频繁维修,提高设备综合利用率。
(5) 隔热保温:真空炉体设计安装有隔热屏,一般用不锈钢板制作,厚度约10~15mm,主要目的是为了提高炉体内不同部位零件温度的均匀性,当然也有节省电能的目的。
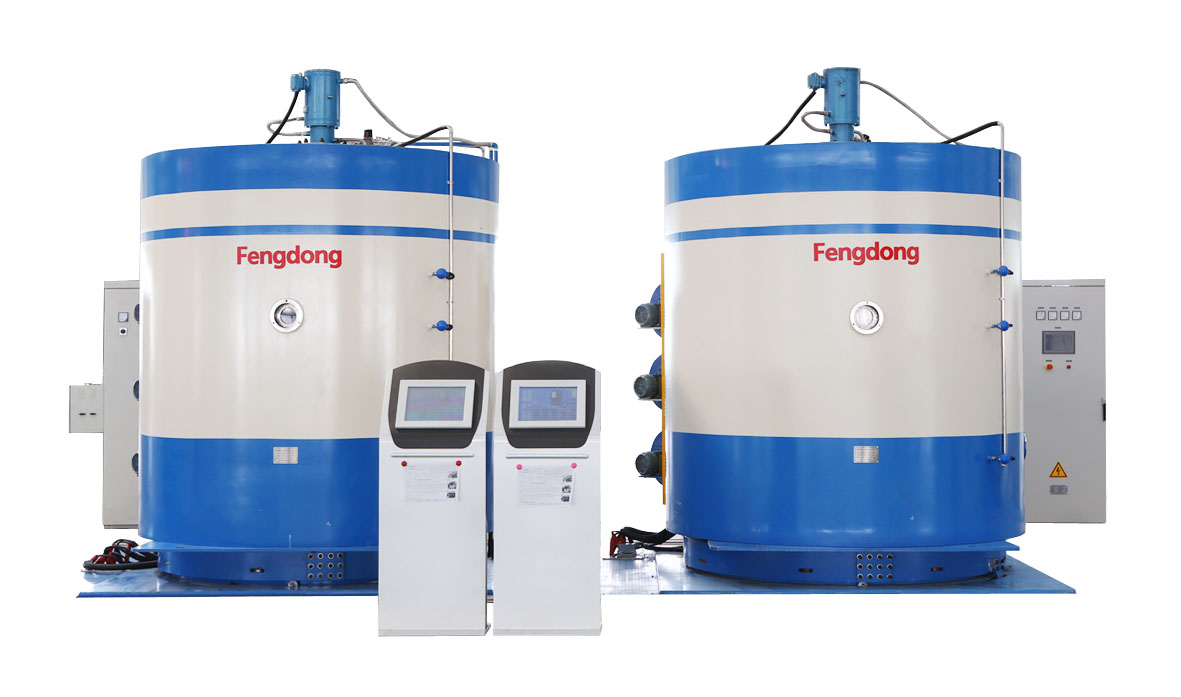
一、白亮层不合格
白亮层是微米级的氮化铁,即Fe2N、Fe3N、Fe4N,常被称作化合物层,因其在显微镜下观察时呈白亮的颜色,所以又称作白亮层。白亮层也是单纯的ε相,其耐磨性很好,所以化合物层可以改善抗咬合性、耐磨性、抗腐蚀性能。
某公司零件的白亮层要求3~10μm,曾出现无白亮层或白亮层只有1~3μm的问题,该问题最终锁定在炉子的密封性,主要是因为质量流量计和电磁阀之间的连接处漏气而造成的。白亮层不合格的常规分析方法如下:
1、渗氮气氛的影响
离子渗氮气氛中氮和碳的含量是影响化合物层相结构的重要因素。
气氛含氮量对化合物层相结构的影响:随着气氛含氮量增加,化合物层中ε相增多,白亮层也随之增厚,根据经验最佳的N2:H2比例为4:1。含碳量对化合物层的影响:气氛中添加含碳气体将抑制γ相形成,而得到以ε相为主或ε单相结构的化合物层。如气氛中加入丙烷(C3H8)后,化合物层中ε相含量迅速增多,基本由ε单相组成。含碳量再增加则化合物层中开始出现Fe3C;含碳量继续增加,则Fe3C 增多,ε相就会减少直到完全消失。离子渗氮需要严格控制气氛中含碳量,使之能得到ε单相或ε+少量Fe3C的双相组织。这样的组织其硬度和耐磨性均比单纯离子氮化有较大提高。
2、钢材成分和组织的影响
随着钢中含碳量及合金元素增加,氮化层中ε相也随之增多。基体组织硬度较高者,渗氮层表面硬度也较高,而且化合物层较厚,其中ε相也较多。一般来说,调质组织渗氮后化合物层中的ε相含量比正火组织的少。
3、渗氮保温时间的影响
有些钢化合物层厚度在渗氮初期增长较快,保温2~4h后变化不大。而38CrMoAl钢化合物层厚度则随时间延长而增厚,保温24h后,这种趋势仍然保持着。所以保温时间对化合物层的影响程度要根据平时调试设备时的经验来总结,每种产品在不同的设备中会有些差异。
4、渗氮温度的影响
40Cr 钢渗氮时,从500℃上升到560℃,化合物层中ε和γ'均增加;当上升到580~600℃时,ε相忽然减少,γ'相数量猛增;当温度上升到620℃时,γ'相数量急剧减少;而当温度上升到650℃以上时,则化合物层分解。这点也是要积累调试验,做好设备档案,供分析问题时参考。
5、气压的影响
离子渗氮的化合物层厚度在某一最佳气压下出现最大值,氮化物ε相的含量和气压也有类似的关系。如27CrMnTi 钢在530℃渗氮,气压为100Pa左右时,化合物层中ε相含量最多;如果气压值上升到120 Pa以上时,化合物层则会急剧减少。
6、设备的密封性的影响
如果炉内进入空气,空气中大量的O2会优先与Fe形成化合物,就会直接影响氮化物ε相的形成。离子氮化是在低压状态下生产的,小于环境的压力,所以炉子的密封性非常重要,否则在真空泵连续工作的作用下,空气就渗入炉内了。设备的主要漏气点有:罩盖的密封处、热电偶的密封处、工艺气体输送途中的各连接处、真空泵阀、质量流量计接头部位或其他密封部位。钟罩式离子氮化设备的压升在实际生产中最好≤0.12 Pa /min(要憋压30 min 以上) ,设备作业指导书要明确操作者需定期憋压检查炉子的密封性。
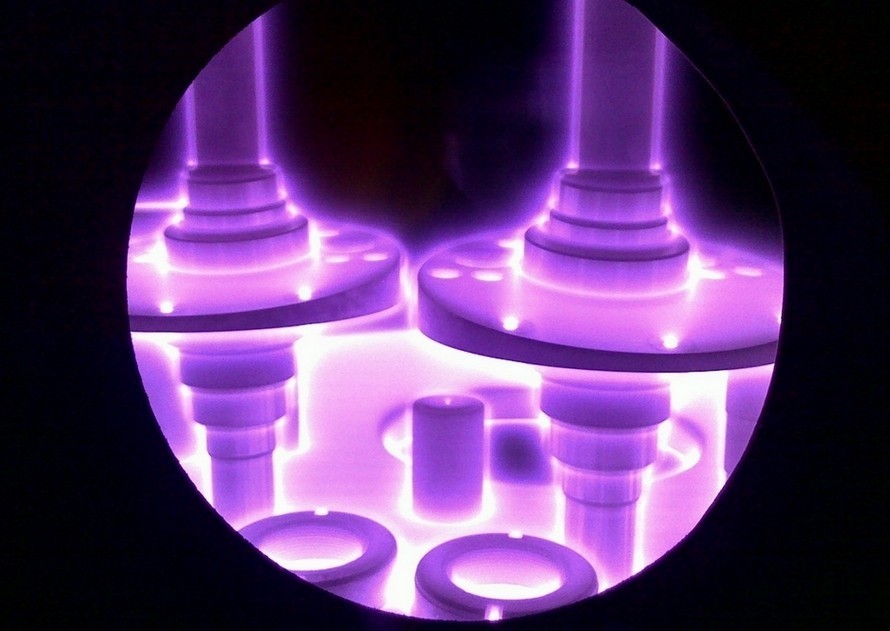
渗氮层硬度高而且表层处于压应力状态,能显著提高钢的耐磨性与疲劳强度,改善耐蚀性和抗擦伤性能,所以氮化层不足或不均匀是零件的重要质量缺陷。实际生产中经常会遇到无氮化层或层深不合格的问题,主要原因分析如下:
(1) 渗氮温度偏低,保温时间不够在生产中,如果因仪表控制不当,未能达到工艺要求的温度,而保温时间仍按工艺文件执行;或渗氮温度是正确的,而渗氮时间小于工艺文件规定的时间,都可能造成渗氮层不足。所以在生产中要定期校验仪表,严格控制工艺参数,按工艺要求执行。
(2) 活性N 原子不足
如果氮氢比例不当,氮原子偏少,则在炉中可供渗氮的离子过少,会降低渗氮速度,使渗氮层的深度降低。还有设备打弧严重,也会使活性N 原子数量降低,(5) 中将详述。
(3) 零件装夹不合理
如果零件装夹不当,例如摆放位置不合理、装炉量太大,都会造成温度不均匀,温度偏低处的层深则减少;还有如果零件摆放太近,会影响辉光离子的流动,从而降低了氮化速度。这两点都会造成层深不足或不均匀的问题,合理的装炉方式需要根据生产实践和经验的积累来确定。
(4) 炉子密封性不好、漏气
与影响白亮层一样,这点也是渗氮层不足的重要原因,空气的进入会直接影响氮原子的吸收和扩散,这点工程技术人员悉知。
(5) 设备打弧
零件装炉完毕,罩上炉罩,开启真空泵抽真空,待真空度抽至50Pa以上后,即可通电起辉。整个离子氮化工艺过程大致分为打散弧清理、升温、保温三个阶段。实际生产中,打弧现象主要集中在前两个阶段,如果电压、峰值电流正常,不打“死弧”,工艺能顺利通过,则对零件的质量影响不大;如果在保温阶段频繁打弧,且打弧严重影响到峰值电流、占空比等工艺参数使其波动异常,就会直接影响零件的质量,所以要求在保温阶段有一组相对稳定的工艺参数值。
对于全自动控制的离子氮化炉,操作者应能正确地判断各种不同的打弧情况,适时进行手动干预,这对维持正常生产是非常必要的。手动干预的主要方式有适当降低电压、气压,使打弧电流减小,直到打弧停止,如果手动调整不能停止严重打弧,此时最大电流已不能维持工件升温、保温的需要。就必须停泵吊起炉罩,看清打弧源的位置,消除引起打弧的根源,才能重新恢复工艺过程。
生产实践中总结打死弧的主要原因有:装炉量过大(即负载过大,峰值电流会急剧升高) 、小缝小孔处、电绝缘位置失效等。要想确保零件质量,打死弧时需要及时停炉处理。
(6) 温度差异与毛坯组织的影响
温度差异和毛坯组织不理想是引起渗氮层不均匀的主要原因。如果炉内上、中、下层温度不均匀,控温不好,会使同一炉的不同位置零件出现层深的差异,因此热电偶的安装位置、辅热的布置、热电偶的定期标定等工作就显得尤为重要了。试验证明,如果零件毛坯组织不均匀,出现严重的带状组织,晶粒粗大,都会使零件氮化后层深、硬度出现不均匀的现象。理想毛坯要求:带状组织为A 级;晶粒度控制在8~9 级。
(7) 零件的清洁度影响
零件清洗不干净,表面有清洗剂等残留物,会影响氮原子的吸收甚至无法渗氮,还会引起严重打弧,所以零件表面清洁是保证渗氮产品合格的前提和基础,是关键点。
理想的清洁方式是采用两次清洗,第一次用普通清洗剂清洗零件表面的油污,暂时不烘干;第二次用脱离子水清洗,清洗浓度要控制在1% 以内,且只能用吹气的方式将零件吹干,保证零件表面清洁、无任何残留物。
离子氮化设备结构复杂,工艺控制困难,在出现问题时借鉴他人的经验能使问题得到快速解决。青岛丰东热处理有限公司专注于离子氮化设备制造与离子氮化热处理工艺研发,在不断的探索和实践中积累了大量的经验,希望能与各位离子氮化人士进行沟通和交流。
- 上一篇:等离子渗氮工艺原理及离子轰击过程
- 下一篇:离子渗氮技术与设备展望